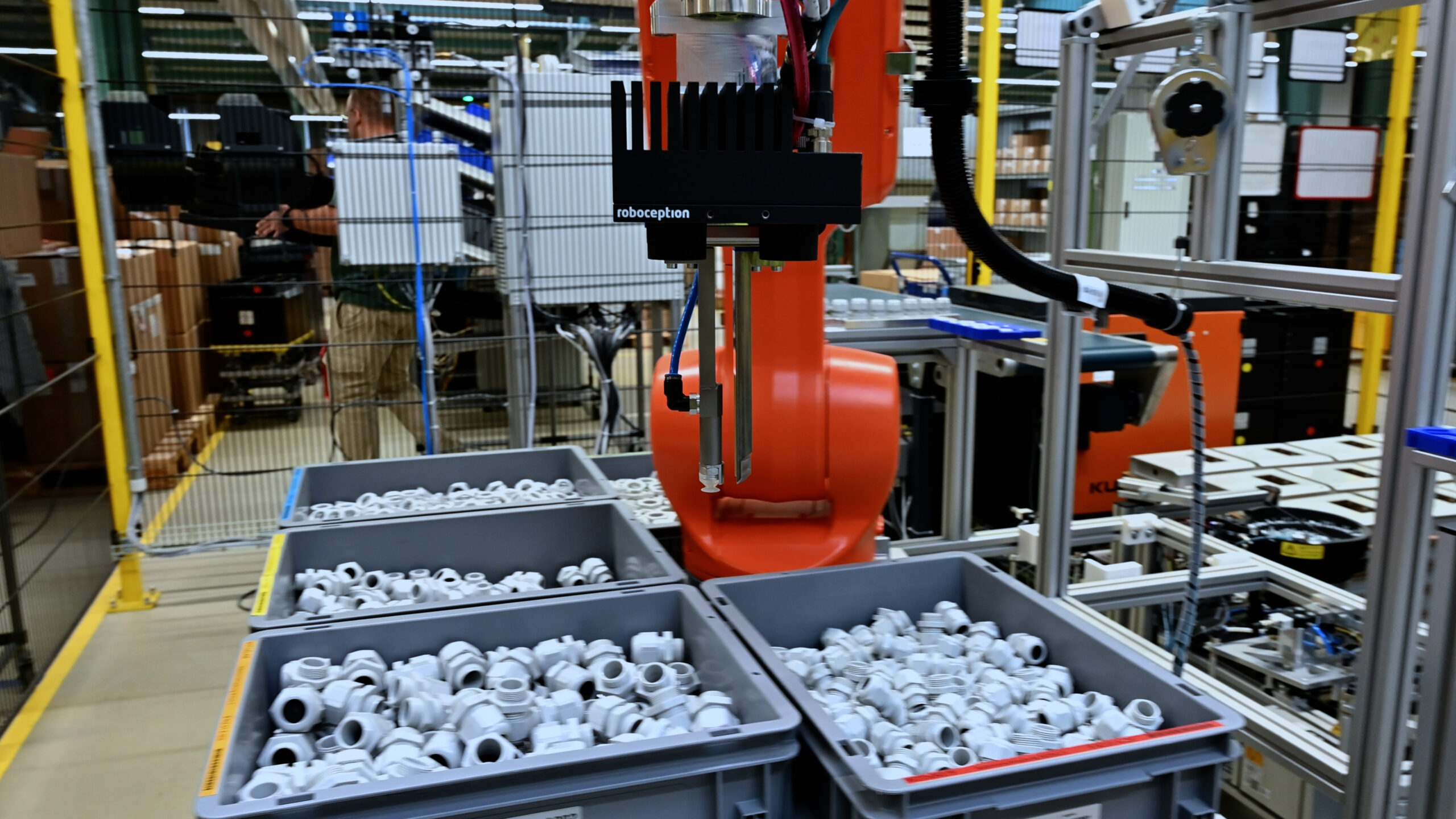
3D Camera Replaces Manual Picking and Saves Space
How a once tedious manual assembly process was reliably automated while minimizing the required floor space.
“Despite the major challenge of automatically recognizing more than 100 components for these pick-and-place tasks, thanks to using robot vision for machine tending processes we solved the issue in a highly satisfactory manner – and provided our customer with the perfect solution.“
Olav K. Sjørslev, Sales Manager at QRS
As personel is becoming increasingly scarce, supply chains increasingly complex and shopfloor space increasingly costly, the ability to efficiently automate low-value-add tasks such as machine tending with little to no manual intervention in the necessary pick-and-place process is becoming a competitive advantage across industries.
At Danfoss, a Danish manufacturer of mobile hydraulics as well as electronic and electrical components, robotic systems equipped with 3D robot vision sensors now reliably and precisely recognize and move a large number of different components.
In the new production line implemented by Danish integrator Quality Robot Systems (QRS), a total of six KUKA robots take over work steps that were previously performed manually. For this, the robotic cells must recognize and move up to 100 different components with no manual intervention.
“The requirement for the robotic cells at Danfoss was a fully automatic feeding of the components with no manual intervention. Obviously, this task can only be solved with a robot vision system, given the large number of variations,” explains Olav K. Sjørslev, Sales Manager at KUKA integration partner QRS.
The alternative, namely feeding the blanks meticulously ordered and aligned, was simply not economically feasible.
Instead, the objects arrive at the first robot station in standard roll boxes. They are sorted by box, however, the boxes are stacked on top of each other more or less indiscriminately. Furthermore, paper sheets seperate the layers of objects.
To meet the challenges of object recognition, QRS benefited from its close partnership with KUKA. For when it comes to robot vision systems, pick-and-place requirements and object recognition, KUKA turns to its Munich-based partner Roboception and their rc_visard 3D stereo sensor.
At Danfoss, the rc_visard (using the SilhouetteMatch software), reliably detects the position and orientation of the flat, unordered objects on the flat paper surface. It also provides the robot with the grasp points for the pick-and-place process at the same time.
A 2D solution was quickly ruled out for this machine tending project: The paper slipsheets are not always completely flat, or may be oily due to the components. In tests with other systems, the camera had sometimes misinterpreted imprints as workpieces. SilhouetteMatch, on the other hand, recognizes exactly which components are supplied to the robotic cell. It reliably transmits the appropriate grasp points for a KR CYBERTECH from KUKA.
“Before this project, our experience with camera systems in the past was not particularly good. We looked into various systems over the past decade, but did not find a single 3D vision solution that met our needs.
What works at a trade fair or in a manufacturer’s demonstration room is often not viable under real-world conditions.”
Quality Robot Systems (QRS) is a Danish KUKA System Partner and expert in industrial robotic automation that can take care of everything from the initial planning and design to the delivery, installation and servicing of a new robot cell. About 35 employees work from headquarters in Vissenbjerg and on-site at customer sites throughout Denmark. A large subcontractor base helps create and supply peripheral equipment for the automation systems.
The rc_visard 160 is ideally suited for static mounting above a workspace: It is designed for viewing distances of more than 50 cm.
The rc_randomdot pattern projector enhances the setup for ideal detection results even for the more tricky objects. It ensures a reliable detection in all lighting conditions.
This software module enables the rc_visard to determine position and orientation of comparatively flat objects that are positioned on a plane. It is perfectly suited for this challenging application.
How a once tedious manual assembly process was reliably automated while minimizing the required floor space.
How a high-performance robot vision system solved the pick-and-place performance issues of an automated kitting cell
How adding a robot vision system led to increased robustness and 50% reduced cycle time in refractory bricks production processes
How RG Technologies added automatic contour detection as a key USP into their software solution for leather processing
How a once tedious manual assembly process was reliably automated while minimizing the required floor space.
You would like to find out whether our portfolio is suitable for your robotic application? Simply request a feasibility study free of charge, and get a live demo of our products.
Would you like to try out one of our sensors and software solutions? Our Try-&-Buy-option gives you the chance to test our products before you decide, and to be sure you make the right choice for your application.