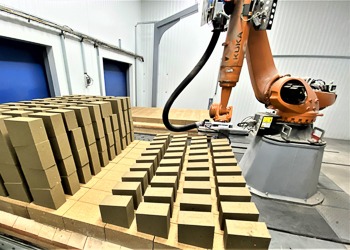
Robot Vision System Improves Industrial Automation
How adding a robot vision system led to increased robustness and 50% reduced cycle time in refractory bricks production processes
The rc_reason BoxPick depalletizing software module is an optional on-board component of the rc_visard that provides a perception solution for robotic pick-and-place applications such as de-/palletizing and sorting of packages. It allows the detection of stationary objects with rectangular surfaces and the determination of their position, orientation and size for picking.
The rc_reason BoxPick module is an optional software component that can be easily installed on one of our smart 3D stereo sensors or the rc_cube Edge Computer, and operated through the sensor’s standard interface. Equipped with the BoxPick Module, the sensor detects rectangular surfaces over predefined size ranges and optionally computes potential pick points. It allows the detection of the position, the orientation and the size of the stationary objects and enables the robot to place the objects in a defined position.
The use of the rc_randomdot projector is mandatory in order to support all kind of surfaces, especially of packets whose natural scene texture is insufficient. The ExposureActiveAlternate mode of the Projector sets the output high during the exposure time for each frame, so that the quality of the depth image is improved for every image.
The BoxPick module enables robots to pick unsorted and unordered packets out of a bin and palletize these items in a defined orientation. It can also be used to depalletize parcels on a conveyor belt, e.g. for cross-belt sorters.
The BoxPick solution excels at accurately identifying box-shaped objects defined by their dimensions, offering a versatile approach that accommodates both rigid and flexible items. This adaptability ensures a comprehensive solution for the diverse objects encountered in material handling processes. Enhanced with the innovative +Match extension, it demonstrates an advanced ability to detect and identify multiple rectangles with identical appearance.
This exceptional feature enhances the effectiveness of pick-and-place applications for this type of product, making it particularly suitable for a wide range of scenarios involving printed product packaging, labels, brochures, books, or any other rectangular objects decorated with distinctive prints or patterns.
A notable feature of the +Match extension is its remarkable ability to generate templates by recognizing textured rectangles of predefined sizes. Once created, these templates are not just a one-time asset, but can be systematically reused for subsequent identifications. Each template has the capacity to store up to ten different “views” representing a variety of prints or textures associated with different objects. This unique functionality proves invaluable in scenarios where the challenge is to organize stacks of magazines that have the same dimensions but different imprints.
For those who want to harness the power of the +Match extension, it is available through a separate license, providing not only the flexibility, but also the scalability required to meet diverse operational needs. This standalone licensing approach enables seamless integration into existing systems and processes, improving the overall efficiency of robotic vision in material handling and related applications. As an integral part of the rc_reason software suite, the +Match extension plays a pivotal role in taking robotic vision capabilities to unprecedented heights, revolutionizing the object handling capacities of robots with its advanced features and adaptability.
How adding a robot vision system led to increased robustness and 50% reduced cycle time in refractory bricks production processes
Hardware requirements | Any compatible 3D stereo sensor (plus rc_cube as needed) rc_randomdot Projector and IOControl Module Robotic system equipped with suction/grasping device |
Grasp computation time | 1 to 3 seconds (depending on object and scene) |
Capturing mode | One-shot mode |
Note that the BoxPick Module does currently not automatically deliver collision-free grasp points for two-finger grippers when objects are stacked side-by-side with no gaps. Such an application will require individual programming on the robot side. Please contact us to discuss details! |
For more detailed information about our products and our software modules for your robot vision solution, please visit our Knowledge Base:
You would like to find out whether our portfolio is suitable for your robotic application? Simply request a feasibility study free of charge, and get a live demo of our products.
Would you like to try out one of our sensors and software solutions? Our Try-&-Buy-option gives you the chance to test our products before you decide, and to be sure you make the right choice for your application.