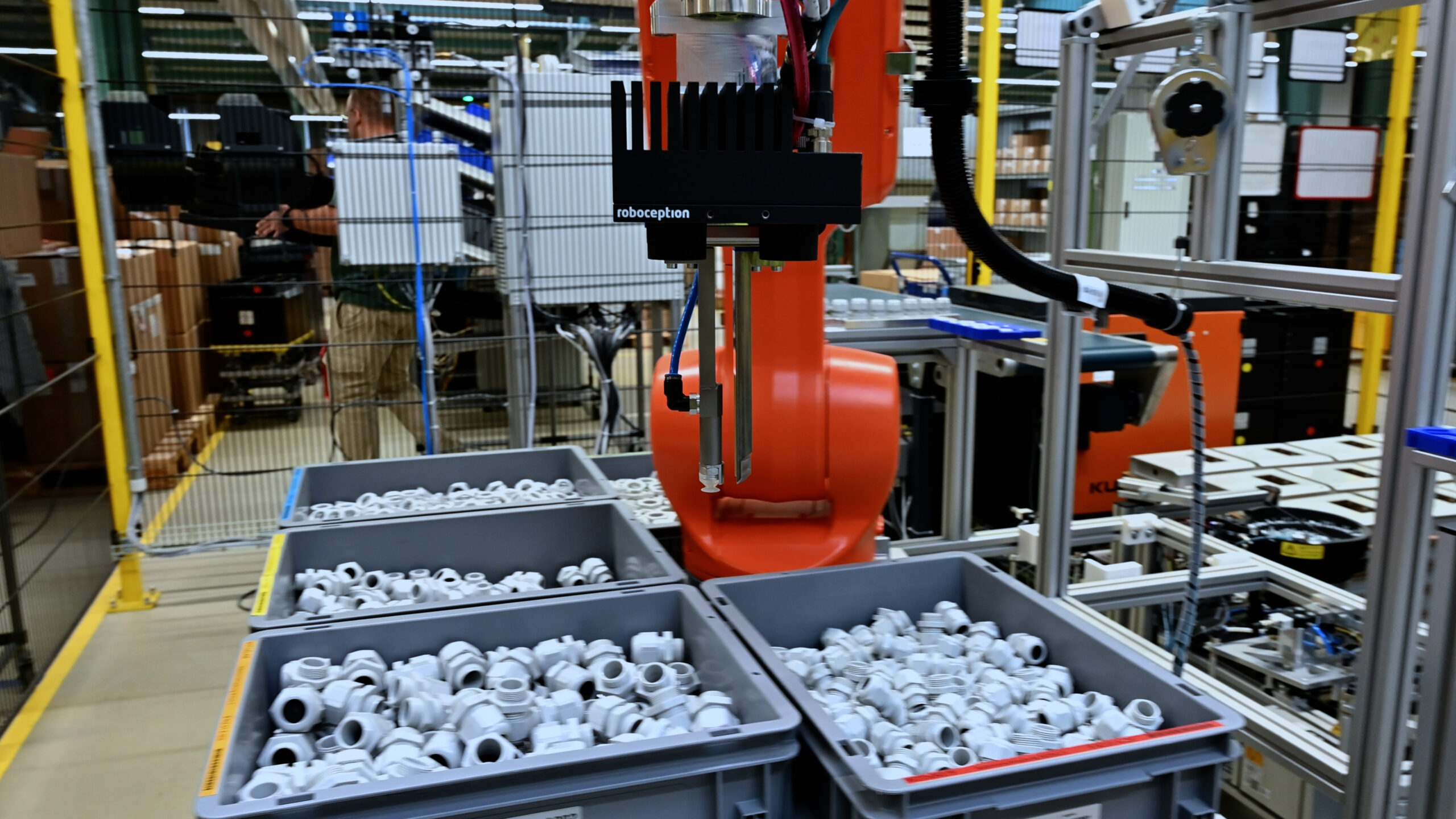
3D Camera Replaces Manual Picking and Saves Space
How a once tedious manual assembly process was reliably automated while minimizing the required floor space.
When it comes to automating processes in laboratories, the potential is significant, but the challenges are many. Robotic systems must be able to handle delicate goods, work in the absence of humans as well as alongside them, and be flexible enough to adapt to regularly changing environments and tasks. Therefore, the ability to perceive the environment and precise localization are key in such sensitive environments. At the same time, reliability and robustness are absolutely essential in order not to jeopardize the often sophisticated processes.
Founded in 2003, laboratory automation specialist Biosero’s first project was to help a pharmaceutical company automate its laboratory. Since then, Biosero’s teams have been working to support scientists with “automation that works”, with accessibility and robustness as the cornerstones of their solutions.
While developing a mobile robotic solution for moving labware between workstations and instruments within laboratories, the team encountered a challenge: The 5 cm position repeatability of their mobile base was sufficient for navigating the robot through the lab environment. However, it was simply not precise enough to support the pick-and-place operations of highly sensitive labware. For this, they needed a much more precise localization, with an accuracy of 1 mm (!).
“We therefore needed a way to localize the arm with respect to the pick-and-place position. After extensive research, we decided upon using a method of pairing a fiducial with the pick-and-place position, as this is fast and non-invasive,” explains Rob Harkness, CTO at Biosero. After evaluating a number of different camera solutions that provide out-of-the box solutions for hand-eye-calibration and the detection of fiducials, QR Tags, or AprilTags, the team decided to use Roboception’s rc_visard and the supporting TagDetect software module.
One decisive factor: The rc_visard 65 delivers a highly precise localization even at a 100 cm working distance, where it achieves a pose precision of 0.7 mm. This turned out to be critical, as the sensor must be mounted quite high on the Brooks PF-400 SCARA arm. This way, it would not obstruct the arm’s path into the laboratory infrastructure that it is picking and placing from.
“The rc_visard is an essential element in guiding our Mobile Robot product.
Its reliability in the ever-changing laboratory environments we operate in has been crucial, and we are confident that we made the right choice for this task"
In addition to the sensor’s meeting their precise localization requirements, Biosero’s teams appreciate that “the documentation from Roboception is fantastic and we have always found the support team to be very responsive”. They believe that “Roboception’s products will continue to be valuable in our future endeavors, as they allow us to develop innovative and efficient lab automation solutions for a wide range of applications”.
Biosero is a leading provider of lab automation solutions, specializing in the development and implementation of cutting-edge technology to optimize laboratory workflows. The company’s innovative solutions are designed to increase throughput and minimize human error in various laboratory environments.
The necessary detection capabilities and performance, coupled with an attractive cost/benefit ratio, as well as the high level of service of the Roboception team were considered when Biosero selected the rc_visard 65m.
The rc_reason TagDetect module is part of the standard software package of the rc_visard. It provides robust detection of QR codes and AprilTags and calculates the 3D position and orientation of each tag relative to the sensor.
How a once tedious manual assembly process was reliably automated while minimizing the required floor space.
How a high-performance robot vision system solved the pick-and-place performance issues of an automated kitting cell
How adding a robot vision component enables precise pick-and-place for automated machine tending with 100+ different parts
How adding a robot vision system led to increased robustness and 50% reduced cycle time in refractory bricks production processes
How a once tedious manual assembly process was reliably automated while minimizing the required floor space.
You would like to find out whether our portfolio is suitable for your robotic application? Simply request a feasibility study free of charge, and get a live demo of our products.
Would you like to try out one of our sensors and software solutions? Our Try-&-Buy-option gives you the chance to test our products before you decide, and to be sure you make the right choice for your application.