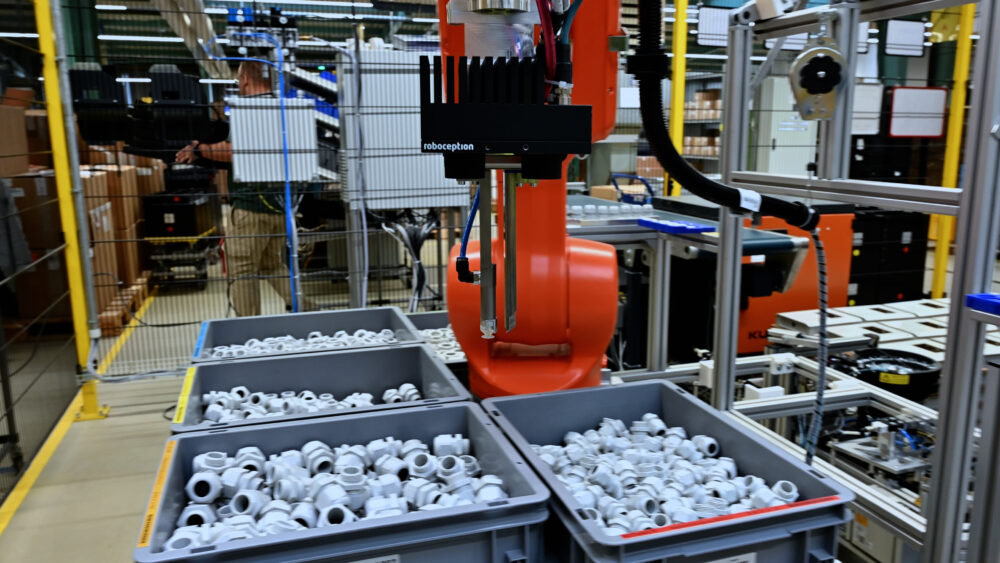
3D Camera Replaces Manual Picking and Saves Space
How a once tedious manual assembly process was reliably automated while minimizing the required floor space.
The rc_reason CADMatch machine tending software module uses a CAD model as input, AppliedAI-based machine learning techniques for ensuring reliable detection, and highly intuitive user interfaces for ultimate usability. The module enables a robotic system to reliably detect, locate and pick objects from unmixed load carriers, completely independent of the object‘s position and orientation.
The user can easily configure the grasp points on any trained object through the WebGUI and add additional information about the load carrier and gripper for a complete visualization of the point cloud and potential collisions.
This software solution can significantly increase the efficiency of production processes, for example by automating machine tending, kitting processes or assembly operations.
The highly intuitive interface allows even non-experts to configure the grasp points and implement the pick-and-place process with just a few mouse clicks. The software supports the specification of one or more grasp points per object, hence enabling picking with a two-finger gripper or a suction device.
This module runs off-board the rc_visard or rc_viscore on an rc_cube IPC (not included) or on-board the rc_visard NG, and is operated through an intuitive WebGUI interface that includes a grasp-teaching interface. Note that the purchase of an rc_cube computer is required in order to operate the CADMatch module with an rc_visard or rc_viscore.
The CADMatch machine tending software module requires a template of the object to be detected. This serves as input to an AppliedAI-based detection process. The creation of this template from the object‘s CAD data is available as a service from Roboception; the first two templates are included with the software purchase. Feasibility studies can also be requested via our Customer Area.
Hardware requirements | rc_visard NG, rc_viscore or any rc_visard sensor rc_cube: Off-board installation required, use of rc_cube edge computer mandatory with rc_visard and rc_viscore (not needed for rc_visard NG) Robotic system equipped with grasping device |
Minimum object size (recommendation) | Indicative minimum object sizes at different viewing distances: rc_visard 65 (c/m): rc_visard 160 (c/m): rc_visard 160-6 (m): rc_visard NG: rc_viscore 210-m: For smaller objects or greater viewing distances, please consult with us prior to your purchase. |
Grasp computation time | 1 to 3 seconds (depending on object and scene) |
Examples for latencies | 683 x 502 @ 250 ms 1024 x 752 @ 310 ms 2048 x 1504 @ 560 ms 4096 x 3008 @ 1100ms |
Capturing mode | One-shot mode |
How a once tedious manual assembly process was reliably automated while minimizing the required floor space.
How a high-performance robot vision system solved the pick-and-place performance issues of an automated kitting cell
For more detailed information about our products and our software modules for your robot vision solution, please visit our Knowledge Base:
You would like to find out whether our portfolio is suitable for your robotic application? Simply request a feasibility study free of charge, and get a live demo of our products.
Would you like to try out one of our sensors and software solutions? Our Try-&-Buy-option gives you the chance to test our products before you decide, and to be sure you make the right choice for your application.