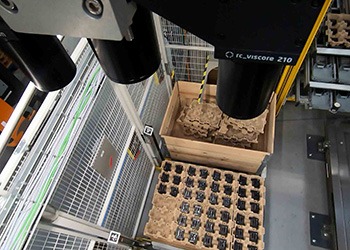
Robot Vision Optimizes Automated Kitting Cell
How a high-performance robot vision system solved the pick-and-place performance issues of an automated kitting cell
nexxos GmbH of Gersthofen, Germany, focuses on individual industrial automation solutions with camera-guided robotics and cobot applications – from first concept to final integration and assembly.
When their customer requested an end-to-end automation of the assembly of an electrical housing – a process that had been performed manually until now – they faced a long list of challenges. Mounting printed circuit boards into a plastic housing seemed comparatively simple. The installation of three different cable glands that are fixed with two different nuts proved to be trickier. The fact that – for logistical and economic reasons – these elements are supplied into the cell as bulk material in chaotic, unmixed bins did not exactly make matters easier.
Add the fact that in today’s automation projects, not only time is money, but space is money as well. And enter Roboception’s 3D vision solutions:
“The hardware and software of Roboception provided the perfect flexible solution for our challenge to replace manual picking.
We mounted the rc_visard 3D-camera system on the gripper of an Agilus for separating five different parts from bulk material in boxes. The whole system has a footprint of less than one square meter.”
In order to save a considerable amount of space as well as money, the nexxos team decided against the traditional solution of using a vibrational feed to separate the parts. Rather, they equipped their KUKA KR6 R900-2 Agilus with a robot-mounted rc_visard 65m stereo camera. The supporting rc_reason CADMatch software module runs on an rc_cube IPC.
The robot routinely accesses five load carriers, using the robot-mounted rc_visard to acquire an image of the respective load carrier and identify the best grasp point for the robot’s picking of the required part.
“This solution not only minimizes the required floorspace to less than one square meter,” says Stefan Briefi. “It also makes the system flexible: In case a part should change, all that is needed is for a new CADMatch template to be implemented into the routine.”
Briefi appreciates this high amount of flexibility, as well as the high level of sophistication of the software components: “The software perfectly met the requirements to the last detail. What’s more, it is easy to operate through intuitive menus and settings – a real plus!”
He is convinced that nexxos will call on Roboception’s portfolio again in the future – and certainly when it comes to “part separation and bin picking of complicated parts”.
nexxos GmbH is an owner-managed robot systems specialist founded in 2021 and based in Gersthofen. The company aims to give customers a decisive competitive advantage through customized automation solutions.
Customer’s production systems are scaled, processes adapted or work steps optimized. The nexxos team contributes specialist knowledge and a wealth of experience in the fields of robotics, plant engineering, mechatronics, camera recognition and PLC.
The necessary detection capabilities and performance, coupled with an attractive cost/benefit ratio, as well as the option to mount the sensor as an end-of-arm tool, were considered when nexxos selected the rc_visard 65.
The rc_reason CADMatch Module relies on an object‘s CAD data. It enables the robotic system to reliably pick a variety of objects from unmixed load carriers. Furthermore, it easily copes with changes in the object‘s position and orientation.
The rc_cube IPC runs the CADMatch Module, enhances the overall performance in industrial applications requiring high-speed image processing and – thanks to the UserSpace – further increases the system’s flexibility.
How a high-performance robot vision system solved the pick-and-place performance issues of an automated kitting cell
How adding a robot vision component enables precise pick-and-place for automated machine tending with 100+ different parts
How adding a robot vision system led to increased robustness and 50% reduced cycle time in refractory bricks production processes
How RG Technologies added automatic contour detection as a key USP into their software solution for leather processing
How a high-performance robot vision system solved the pick-and-place performance issues of an automated kitting cell
You would like to find out whether our portfolio is suitable for your robotic application? Simply request a feasibility study free of charge, and get a live demo of our products.
Would you like to try out one of our sensors and software solutions? Our Try-&-Buy-option gives you the chance to test our products before you decide, and to be sure you make the right choice for your application.